Introduction
In the relentless pursuit of advancing computational technologies, the emerging field of spintronics stands out, promising to redefine the landscape of electronic devices with its innovative use of the electron’s spin in addition to its charge. Central to this scientific and technological revolution is Yttrium Iron Garnet (YIG), a material whose exceptional magnetic properties are propelling the development of energy-efficient and high-speed computing systems. This article explores the role of YIG thin films in spintronics, offering insights into their fabrication, applications, and potential to revolutionize information processing.
The Essence of YIG in Spintronics
Background on Spintronics: Spintronics, or spin electronics, exploits the spin and charge of electrons to create devices that can store and manipulate information with unparalleled efficiency. Unlike conventional electronics, which rely solely on electrical charges, spintronic devices offer the promise of faster processing speeds and lower power consumption.
Why YIG Matters: YIG’s low magnetic damping and high thermal stability make it an ideal material for spintronic applications. Its ability to propagate spin waves over long distances without significant energy loss is particularly valuable in creating devices that are not only faster but also more energy-efficient than current technologies.
Fabrication of YIG Thin Films
Challenges and Solutions: Crafting high-quality YIG thin films is fraught with challenges, primarily due to the material’s complex crystal structure and the need for precise control over its magnetic properties. Advances in deposition techniques, such as pulsed laser deposition (PLD) and magnetron sputtering, have significantly improved the ability to produce YIG films that meet the stringent requirements of spintronic devices.
Innovations in Fabrication: Recent breakthroughs in fabrication technologies have enabled the creation of YIG films with thicknesses ranging from a few nanometers to several micrometers, opening new avenues for their application in various spintronic devices. These advances not only enhance the material’s intrinsic properties but also facilitate its integration with other materials, expanding the potential for innovative hybrid devices.
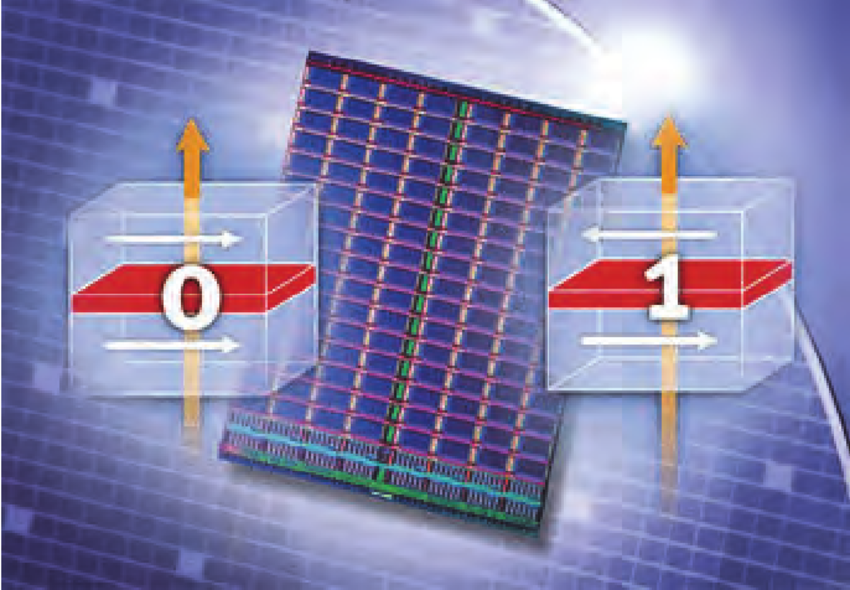
Applications in Spintronics
Spin-Wave Logic Devices: Utilizing YIG thin films, researchers are developing spin-wave logic devices that use the interference patterns of spin waves to perform computational operations. These devices represent a significant leap forward, potentially enabling the construction of computers that operate on the principles of wave physics rather than traditional electronic circuits.
Magnon Spintronics: YIG’s exceptional properties are also being harnessed in the field of magnon spintronics, where the focus is on controlling magnons – quanta of spin waves – for information processing. YIG thin films are pivotal in creating magnonic crystals and circuits, which could lead to the development of ultra-fast and energy-efficient magnonic computing systems.
Beyond Computing: The applications of YIG thin films extend beyond traditional computing. They are crucial in developing sensors, memory devices, and oscillators that leverage spin dynamics for enhanced performance, showcasing the versatility and broad impact of YIG in next-generation technologies.
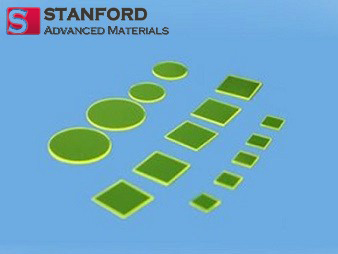
The Future and Beyond
Challenges Ahead: Despite the promising advancements, several hurdles remain in fully harnessing YIG’s potential in spintronics. Issues such as interface quality, integration with semiconductor technologies, and scalability need to be addressed to transition from laboratory breakthroughs to commercial applications.
The Road to Innovation: Ongoing research is focused on overcoming these challenges, with efforts aimed at enhancing the material properties of YIG, developing more efficient fabrication techniques, and exploring novel device architectures. The interdisciplinary nature of this research underscores the collaborative effort required to push the boundaries of what is possible with YIG and spintronics.
Conclusion
Yttrium Iron Garnet thin films stand at the cusp of revolutionizing the field of spintronics, offering a glimpse into a future where computing devices are faster, more energy-efficient, and capable of handling the exponentially growing demands for data processing and storage. As researchers continue to unravel the complexities of this remarkable material, the potential for YIG to transform technology remains vast and largely untapped. The journey from fundamental research to practical applications is long and fraught with challenges, but the promise of YIG thin films in pioneering the future of spintronics is undeniably bright, marking a significant milestone in the quest for next-generation computing technologies.
In this landscape of innovation and discovery, the availability of high-quality raw materials is crucial for advancing research and development efforts. Stanford Advanced Materials (SAM) plays a pivotal role by offering superior quality raw materials necessary for producing high-quality YIG films. Their commitment to excellence ensures that researchers and technologists have access to the materials needed to push the boundaries of what’s possible with YIG thin films. As the field of spintronics moves forward, partnerships with dedicated material providers like Stanford Advanced Materials will be instrumental in turning the theoretical potential of YIG into practical, transformative technologies for the future.