Introduction
Metal powders are pivotal in the world of additive manufacturing, providing the raw materials necessary for 3D printing applications across aerospace, automotive, and medical industries. The choice of metal powder significantly affects the characteristics and quality of the final printed objects. Therefore, understanding the production methods of these powders is essential for ensuring they meet specific industry standards and functional requirements. This article provides a comprehensive overview of different methods used to produce metal powders, each tailored for optimal performance in various 3D printing processes. By examining the nuances of these production techniques, we aim to illuminate how each method influences the properties of metal powders, thereby guiding manufacturers in selecting the most suitable process for their particular needs in 3D printing technology.
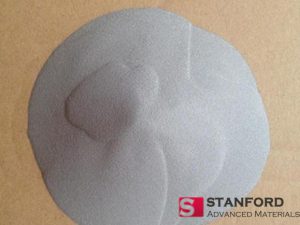
Atomization Method
The atomization process is one of the most prevalent methods for producing metal powders, particularly for 3D printing. This technique involves melting the metal and then dispersing it into fine droplets using a high-pressure fluid medium. As these droplets cool and solidify, they form metal powders of varying sizes, suitable for various additive manufacturing applications.
Gas Atomization: In this variant, a high-pressure gas stream, typically argon or nitrogen, is used to break the molten metal stream into fine particles. The rapid cooling involved in gas atomization helps in obtaining powders with spherical shapes and high packing density, which are ideal for 3D printing due to their excellent flow characteristics and uniformity.
Water Atomization: This method uses high-pressure water to atomize the molten metal instead of gas. Water atomization generally results in slightly irregular powder shapes and larger particle sizes compared to gas atomization. However, it is more cost-effective and can still produce powders suitable for certain types of 3D printing applications that do not require extremely high precision or surface finish.
Solid-State Reduction Method
Solid-state reduction is a pivotal method for producing metal powders, especially for metals where high purity and specific particle characteristics are required. This process involves reducing metal oxides to metals using a reducing agent at elevated temperatures in a solid-state reaction.
The process typically uses hydrogen or carbon monoxide as the reducing agent. These gases react with metal oxides, such as iron oxide or tungsten oxide, to form pure metal powders and water or carbon dioxide as byproducts. The reaction conditions, including temperature and atmosphere, are carefully controlled to optimize purity and particle size.
Materials and Conditions: Common materials produced using the solid-state reduction method include iron, tungsten, and molybdenum powders, which are pivotal in various industrial applications including magnetic materials and high-density parts. The process is conducted in batch or continuous furnaces under a controlled atmosphere to prevent oxidation and ensure uniform reduction.
Specific Metals: This method is particularly beneficial for metals that require high purity and specific morphological characteristics that influence the mechanical properties of the final product. Metals such as tungsten and molybdenum are often produced via this method due to their high melting points, which makes other methods less viable.
Electrolysis Method
The electrolysis method is another effective technique for producing metal powders, particularly suitable for metals that can be deposited from aqueous solutions. This process involves the electrochemical reduction of metal ions in a solution to form fine metal powders.
Process Description: In electrolysis, a metal salt solution acts as the electrolyte. An electrical current is passed through this solution between two electrodes, causing the metal ions to reduce and deposit on the cathode as a solid metal powder. The conditions such as current density, temperature, and electrolyte composition are critical for controlling the particle size and morphology of the powder.
Types of Metals and Applications: Metals commonly produced by electrolysis include copper, nickel, and silver. These powders are used in applications requiring high conductivity and purity, such as electrical contacts and conductive adhesives. Electrolysis is particularly favored for its ability to control the particle structure and purity, which are crucial in electrical and electronic applications.
Advantages and Limitations: One of the significant advantages of the electrolysis method is the high purity of the powders produced, as the metal ions can be selectively reduced and deposited. However, the method’s limitations include high energy consumption and the need for careful disposal or recycling of the electrolytic solutions to prevent environmental contamination.
Electrolysis Method
The electrolysis method is another effective technique for producing metal powders, particularly suitable for metals that can be deposited from aqueous solutions. This process involves the electrochemical reduction of metal ions in a solution to form fine metal powders.
Process Description: In electrolysis, a metal salt solution acts as the electrolyte. An electrical current is passed through this solution between two electrodes, causing the metal ions to reduce and deposit on the cathode as a solid metal powder. The conditions such as current density, temperature, and electrolyte composition are critical for controlling the particle size and morphology of the powder.
Types of Metals and Applications: Metals commonly produced by electrolysis include copper, nickel, and silver. These powders are used in applications requiring high conductivity and purity, such as electrical contacts and conductive adhesives. Electrolysis is particularly favored for its ability to control the particle structure and purity, which are crucial in electrical and electronic applications.
Advantages and Limitations: One of the significant advantages of the electrolysis method is the high purity of the powders produced, as the metal ions can be selectively reduced and deposited. However, the method’s limitations include high energy consumption and the need for careful disposal or recycling of the electrolytic solutions to prevent environmental contamination.
Read more: Metal Powder Materials Used in 3D Printing