Tantalum Overview
Tantalum is part of the refractory metal group and it has good physical and chemical properties.
Tantalum has a high hardness that can reach 6-6.5. Its melting point is as high as 2996 ° C, only after carbon, tungsten, rhenium and osmium. Tantalum is malleable and can be drawn into a thin foil. Its coefficient of thermal expansion is very small, and it only expands by 6.6 parts per million per degree Celsius. In addition, it has strong toughness and is superior to copper.
Tantalum does not react with hydrochloric acid, concentrated nitric acid and “aqua regia” under both cold and hot conditions. And tantalum is only corroded by concentrated sulfuric acid at temperatures above 150 °C. Tantalum can be considered one of the most chemically stable metals at temperatures below 150 °C. It is also highly resistant to corrosion because of the formation of a stable tantalum pentoxide (Ta2O5) protective layer on its surface.
Tantalum Application
Tantalum can be used to manufacture evaporation vessels, as well as tubes, rectifiers, and electrolytic capacitors. Tantalum forms a stable anodized film in an acidic electrolyte. The electrolytic capacitor made of tantalum has the advantages of large capacity, small size and good reliability. Tantalum capacitors are the most important use of tantalum, around 2/3 of the full use of tantalum. Tantalum is also the material for making electron-emitting tubes and high-power tube parts. Anti-corrosion equipment made by Tantalum is used in the chemical industry such as strong acid, bromine and ammonia producing industries. The metal tantalum can be used as a structural material for the combustion chamber of an aircraft engine. Tantalum is easy to form and can be used as support accessories, heat shields, heaters and heat sinks in high temperature vacuum furnaces. Tantalum can also be used as orthopedic and surgical materials. Tantalum sputtering targets and tantalum evaporation materials are important coating materials in physical vapor deposition.
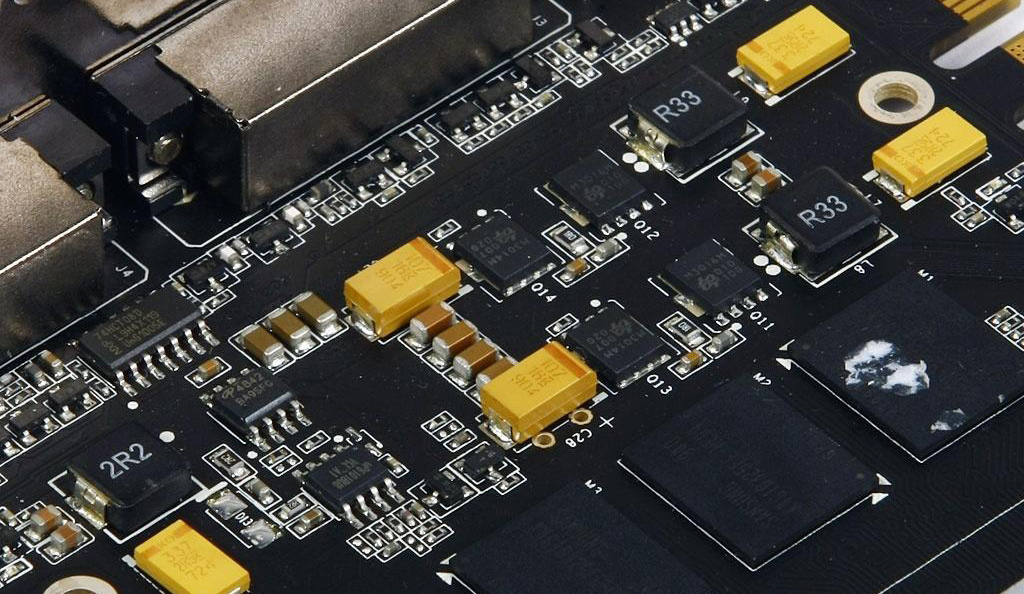
High Purity Tantalum Preparation
The chemical inertness and relatively low price of tantalum make it a good alternative to platinum. However, high-purity tantalum is not easy to get because it is always found together with niobium in the mineral groups of tantalite, columbite, and coltan. To get high purity tantalum, here are several methods.
1 Tantalum powder can be obtained by metal thermal reduction (sodium thermal reduction) method. The potassium fluotantalate is reduced with sodium metal under an inert atmosphere: K2TaF7 + 5Na-→Ta+5NaF+2KF. The reaction was carried out in a stainless steel tank, and the reaction was quickly completed when the temperature was heated to 900 °C. The powder prepared by this method has irregular grain shape and fine particle size, and is suitable for making tantalum capacitors.
2 The tantalum powder can also be obtained by molten salt electrolysis: a molten salt of a mixture of potassium fluoroantimonate, potassium fluoride and potassium chloride is used as an electrolyte, and tantalum pentoxide (Ta2O5) is dissolved therein and electrolyzed at 750 °C. This method can obtain a bismuth powder having a purity of 99.8 to 99.9%.
3 Tantalum can also be obtained by carbothermal reduction of Ta2O5. The reduction is generally carried out in two steps: first, a mixture of a certain ratio of Ta2O5 and carbon is made into tantalum carbide (TaC) at 1800 to 2000 ° C in a hydrogen atmosphere. Then, TaC and Ta2O5 are prepared into a mixture in a certain ratio, and reduced to tantalum in a vacuum.
4 Tantalum can also be obtained by thermal decomposition or hydrogen reduction of chloride. The dense metal crucible can be prepared by vacuum arc, electron beam, plasma beam melting or powder metallurgy.
Please visit https://www.sputtertargets.net/ for more information.