Discovery
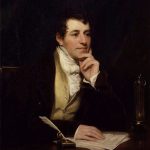
Compared with other metal elements we discussed about before, Aluminum is discovered much later. In 1808, the British chemist Sir Humphry Davy confirmed the existence of alum and named the substance to Alumium (later changed to Aluminum).
In 1825, Danish chemist and physicist Hans Christian Ørsted began experimenting about aluminum extraction. However, it was not until 1827 that Friedrich Wöhler reduced the molten anhydrous aluminum chloride with potassium metal to obtain a purer metallic aluminum element.
As precious as gold
However, as Wöhler’s method could not yield great quantities of aluminium, the metal remained rare; its cost exceeded that of gold. It is for this reason that aluminum was in a high position at that time. It is said that at a banquet, the French emperor Napoleon used aluminum knives and forks alone, while others used silver tableware. Also, the king of Thailand once used an aluminum bracelet.
Mass production
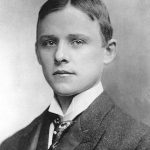
In 1886, French engineer Paul Héroult and American engineer Charles Martin Hall, respectively, independently electrolyzed a mixture of molten bauxite and cryolite to produce metal aluminum, which laid the foundation for large-scale production of aluminum in the future. Since then, the status of aluminum has changed completely, mainly in two aspects: first, it is mass-produced and is no longer regarded as a precious metal; the mass production of aluminum in industrial and domestic applications has gradually replaced the use of other metals such as steel and copper in many fields.
Application Prospect
At present, the aluminum industry has problems such as overcapacity and insufficient utilization, so the development prospects of the aluminum industry in the short term are not optimistic.
However, due to the abundant reserves of aluminum in the earth’s crust and the advantages over other metal elements, aluminum will have extremely broad application prospects in the future. For example, automakers are currently exploring the use of large-area aluminum alloy instead of steel to make the car lighter.
With the advancement of technology, aluminum alloy products will not only grow rapidly in traditional applications such as aerospace, transportation, electronic power, and construction, but will also grow rapidly in other new fields.
This is a history column of SAM Sputter Target, aiming at introducing the history of different metals. If you are a metal lover or history lover, you can follow our website. For previous posts of this column please search the keyword “history”.
Please visit https://www.sputtertargets.net/ for more information.